Where Can You Find the World’s Longest Conveyor Belt System?
When asking, where can you find the world’s longest conveyor belt, the United States boasts some impressive systems. The longest conveyor belts in the U.S. are essential for industries such as mining and agriculture. They span significant distances, connecting various points within industrial operations. Notable examples include the belts used in the mining sector, which transport materials efficiently across vast areas. These conveyor systems are engineered for durability and efficiency, making them vital for large-scale operations. Exploring where can you find the world’s longest conveyor belt reveals the innovative solutions employed in the U.S. to maintain seamless industrial workflows and enhance productivity across various sectors.
Where Can You Find the World’s Longest Conveyor Belt
When considering the marvels of modern engineering, conveyor belts might not be the first things that come to mind. However, these mechanical conveyors are integral to the efficiency and functionality of numerous industries around the globe. Among these impressive constructions, the world’s longest conveyor belt is a standout, located on the African continent, specifically in the Western Sahara.
The Longest Conveyor Belt in Africa
Africa is home to the world’s longest conveyor belt, a remarkable feat of engineering that stretches across the harsh desert landscape of Western Sahara. This belt is part of the Bou Craa phosphate mines, and it serves a critical role in the mining industry by transporting phosphate from the mines to the coast for export. The belt is an impressive 98 kilometers (61 miles) long, making it the longest of its kind in the world.
The purpose of this conveyor belt is to facilitate the movement of phosphate, which is a vital mineral used primarily in fertilizers. Phosphate mining is a significant economic activity in Western Sahara, and the conveyor belt ensures that the mined phosphate can be transported efficiently to the coastal town of El Aaiún, from where it is shipped worldwide.
Length and Structure
Spanning an extraordinary 98 kilometers, the conveyor belt begins at the phosphate mines in Bou Craa and travels across the desert to the port of El Aaiún. The belt is an engineering marvel, designed to withstand the harsh conditions of the desert, including extreme temperatures, sandstorms, and the challenging terrain.
The conveyor belt’s design incorporates robust materials and technologies to ensure its durability and efficiency. It consists of a series of interconnected belts powered by electric motors, supported by a network of pulleys and rollers that keep the belt in motion. The belt is also equipped with various sensors and monitoring systems to ensure smooth operation and to detect any potential issues before they become major problems.
Economic and Environmental Impact
The existence of the world’s longest conveyor belt has significant economic implications for Western Sahara and the surrounding regions. The conveyor belt system drastically reduces the cost and time associated with transporting phosphate from the mines to the port, thereby enhancing the efficiency and profitability of the mining operations.
Phosphate is a key ingredient in agricultural fertilizers, which are essential for global food production. By facilitating the efficient transport of phosphate, the conveyor belt contributes to the global supply of this critical resource, supporting agriculture and food security around the world.
However, the environmental impact of such a massive conveyor belt cannot be overlooked. The belt traverses the fragile desert ecosystem, and the mining activities associated with the phosphate industry can have detrimental effects on the local environment. Efforts have been made to mitigate these impacts, including measures to reduce dust and emissions, as well as initiatives to restore and protect the surrounding landscape.
Technological Advancements
The conveyor belt in Western Sahara represents a significant technological advancement in the field of materials handling and transportation. The sheer length and scale of the belt required innovative engineering solutions to overcome the challenges posed by the desert environment.
One of the key technological features of the conveyor belt is its automated control system. This system allows for real-time monitoring and management of the belt’s operation, ensuring optimal performance and minimizing downtime. Advanced sensors and data analytics are used to track the condition of the belt, detect wear and tear, and predict maintenance needs, thereby enhancing the reliability and longevity of the system.
Maintenance and Operational Challenges
Maintaining the world’s longest conveyor belt is no small feat. The harsh desert environment presents numerous challenges, including high temperatures, abrasive sand, and limited access to resources and infrastructure. Regular maintenance is crucial to ensure the belt operates smoothly and efficiently.
Maintenance activities include routine inspections, lubrication of moving parts, replacement of worn components, and monitoring of the belt’s tension and alignment. The use of advanced diagnostic tools and predictive maintenance techniques helps to identify potential issues early and address them before they lead to costly breakdowns or disruptions in operation.
Future Prospects
Looking ahead, the future of the world’s longest conveyor belt in Western Sahara will likely involve further technological advancements and improvements in efficiency and sustainability. Innovations in materials science, automation, and environmental management will play a key role in enhancing the performance and reducing the environmental impact of the conveyor belt system.
Efforts are also underway to explore alternative methods of phosphate transportation and to develop new technologies that can further optimize the mining and transport processes. As global demand for phosphate continues to grow, the importance of efficient and sustainable transport solutions will become increasingly critical.
Where Can you Find the Worlds Longest Conveyor Belt: the Longest Single Conveyor Belt in the World
The world’s longest single conveyor belt is located in the Western Sahara, in Africa. This conveyor belt, known as the Bou Craa conveyor belt, stretches approximately 98 kilometers (61 miles). It transports phosphate rock from the Bou Craa mine in the Western Sahara to the coastal city of El Aaiún, where the material is loaded onto ships for export.
This conveyor belt is remarkable not only for its length but also for its significance in the global phosphate industry. The phosphate rock mined in Bou Craa is a critical ingredient in agricultural fertilizers, making this conveyor belt a vital component of the global food supply chain.
The Bou Craa conveyor belt, spanning around 98 kilometers (61 miles), is one of the most impressive feats of engineering in the mining and transportation industries. It plays a critical role in the extraction and export of phosphate rock, a key component in fertilizers used globally.
Transport Volume and Capacity
- Hourly Capacity: The conveyor belt has a transport capacity of approximately 2,000 metric tons of phosphate rock per hour. This high throughput is essential to meet the demands of global markets and ensures that the phosphate mining operations can run efficiently without significant delays.
- Annual Transport Volume: On an annual basis, the Bou Craa conveyor belt is capable of transporting around 7.2 million metric tons of phosphate rock. This massive volume is necessary to sustain the supply chain from the mine to the port, where the phosphate is shipped to various destinations around the world.
Operational Details
- Continuous Operation: The conveyor belt is designed to operate continuously, which is crucial for maintaining the steady flow of phosphate rock. Downtime is minimized to ensure that the mine can operate at full capacity, providing a consistent supply of raw materials for the fertilizer industry.
- Maintenance and Monitoring: Given the length and capacity of the conveyor belt, regular maintenance and monitoring are essential to prevent breakdowns and ensure smooth operation. Advanced monitoring systems are likely in place to detect any issues early and allow for prompt repairs, minimizing disruptions.
- Environmental Impact: The conveyor belt reduces the need for heavy truck transport over long distances, which in turn lowers the carbon footprint of the mining operation. However, the mining of phosphate itself does have environmental impacts, including landscape disruption and potential pollution, which are managed through various environmental controls and regulations.
Significance in the Global Market
Phosphate rock transported by the Bou Craa conveyor belt is a critical input for fertilizers used in agriculture worldwide. The high transport capacity ensures that the global market can be supplied with the necessary raw materials to produce fertilizers, supporting food production on a large scale. The reliability and efficiency of this conveyor system are thus not just important for the local mining operations but have global implications for agriculture and food security.
In summary, the Bou Craa conveyor belt is an engineering marvel that supports the large-scale transport of phosphate rock, with a significant capacity that meets the demands of the global agricultural industry. Its continuous operation and high transport volume are essential to the economic viability of the phosphate mining operations in Western Sahara.

Where Can you Find the Worlds Longest Conveyor Belt: World’s Longest Border-Crossing Conveyor
The world’s longest border-crossing conveyor belt is known as the “Belt Conveyor for Bulk Materials, crossing the Moroccan-Mexican border”. This conveyor system stretches across the border between Morocco and the Spanish territory of Melilla in North Africa.
Key Details:
- Location: The conveyor runs from the phosphate mines in Western Sahara (a disputed territory administered by Morocco) to the coast, where the material is then loaded onto ships bound for Spain and other destinations. The conveyor crosses the border between Morocco and the Spanish territory of Melilla.
- Length: The conveyor belt itself is over 7 kilometers (about 4.35 miles) long, making it the longest border-crossing conveyor belt in the world.
- Purpose: The conveyor is primarily used to transport phosphate rock, similar to the Bou Craa conveyor belt. This phosphate rock is a critical ingredient in fertilizers and is an essential export product for Morocco.
- Significance: This conveyor belt is crucial for the efficient and cost-effective transport of phosphate across the border. By using a conveyor system instead of traditional transport methods, such as trucks or trains, the operation reduces costs and minimizes environmental impacts.
- Environmental Considerations: The use of a conveyor belt over this distance and terrain significantly reduces the environmental footprint of transporting bulk materials across borders. It also helps in minimizing the wear and tear on road infrastructure and reduces traffic congestion at the border crossing.
This conveyor system is a vital part of the logistics chain that supports the phosphate industry in Morocco, ensuring that the material can be efficiently exported to global markets. Its role as the longest border-crossing conveyor underscores its importance in facilitating international trade between Africa and Europe.
Where Can you Find the Worlds Longest Conveyor Belt: Compare the Cost with Say a Railway or Road Transport Alternative
Comparing the cost of operating a long conveyor belt, such as the one at Bou Craa in Western Sahara, with alternatives like railway or road transport, involves several factors, including initial capital investment, operational costs, maintenance, environmental impact, and efficiency. Below is a detailed comparison of these transport methods:
1. Initial Capital Investment:
- Conveyor Belt:
- High Initial Cost: The construction of a long conveyor belt involves significant upfront investment due to the need for specialized materials, engineering, and installation over potentially challenging terrain.
- Cost Distribution: While the initial cost is high, it is often spread out over the belt’s long lifespan (typically 20-30 years or more).
- Railway:
- Very High Initial Cost: Building a railway requires even more extensive infrastructure, including tracks, stations, locomotives, and wagons. The cost per kilometer can be extremely high, especially in remote or difficult-to-access areas.
- Long-Term Investment: Railways often have a longer useful life, but the initial capital outlay is usually higher than that for a conveyor belt.
- Road Transport:
- Moderate Initial Cost: The cost of building roads is generally lower than that of constructing railways or conveyor belts. However, it still requires significant investment, especially in remote areas where new roads must be built.
- Vehicle Costs: The cost of purchasing and maintaining a fleet of trucks adds to the initial investment.
2. Operational Costs:
- Conveyor Belt:
- Low Operating Costs: Once operational, conveyor belts have relatively low running costs. They require electricity, but energy consumption is often optimized. Labor costs are minimal since the system is mostly automated.
- Continuous Operation: Conveyor belts can run continuously, which enhances efficiency and reduces the need for large labor forces.
- Railway:
- Moderate to High Operating Costs: Railways require fuel or electricity for locomotives, as well as ongoing maintenance of tracks, stations, and trains. Labor costs are also significant, including train operators and maintenance staff.
- Scheduled Operation: Trains operate on a schedule, which can sometimes lead to inefficiencies, especially if the demand for transport fluctuates.
- Road Transport:
- High Operating Costs: Road transport typically has the highest operational costs due to fuel, maintenance of vehicles, and the need for a large workforce (drivers, mechanics, etc.).
- Flexibility vs. Efficiency: While road transport is flexible, allowing for door-to-door delivery, it is less efficient for bulk transport over long distances compared to conveyor belts and railways.
3. Maintenance Costs:
- Conveyor Belt:
- Low to Moderate Maintenance Costs: Conveyor belts require regular inspection and maintenance, but these costs are generally lower than those for railways or roads. Modern monitoring systems can further reduce maintenance needs.
- Durability: Conveyor belts are designed to withstand harsh conditions, reducing the frequency of major repairs.
- Railway:
- High Maintenance Costs: Railway tracks, signals, and trains require constant maintenance. The costs can be particularly high in regions with extreme weather conditions or heavy usage.
- Specialized Workforce: Maintaining a railway system requires specialized labor, which adds to the cost.
- Road Transport:
- Moderate to High Maintenance Costs: Roads, especially in remote or harsh environments, need frequent repairs due to wear and tear from heavy vehicles. Additionally, vehicle maintenance is an ongoing cost.
- Infrastructure Wear: The more trucks use the road, the faster the road deteriorates, leading to higher long-term maintenance costs.
4. Environmental Impact:
- Conveyor Belt:
- Lower Environmental Impact: Conveyor belts have a lower carbon footprint compared to trucks or trains, as they are more energy-efficient and often powered by electricity, which can be sourced from renewable energy.
- Less Disruption: Conveyor belts cause less environmental disruption compared to roads or railways since they often follow a single, narrow path with minimal impact on the surrounding landscape.
- Railway:
- Moderate Environmental Impact: Railways are more environmentally friendly than road transport in terms of emissions per ton-kilometer, but they still require significant land use and can disrupt ecosystems.
- Potential for Electrification: Railways can be electrified, reducing their environmental impact if the electricity comes from renewable sources.
- Road Transport:
- High Environmental Impact: Trucks produce significant emissions, contributing to pollution and greenhouse gas emissions. The construction and maintenance of roads also contribute to environmental degradation.
- Traffic and Congestion: Increased road use can lead to traffic congestion, which further increases emissions and reduces efficiency.
5. Efficiency and Capacity:
- Conveyor Belt:
- High Efficiency: Conveyor belts are highly efficient for continuous transport of bulk materials over long distances. They can operate 24/7 with minimal interruption.
- Capacity: Conveyor belts can transport large volumes of material consistently, making them ideal for operations like mining where there is a constant need to move bulk materials.
- Railway:
- High Capacity but Less Flexibility: Railways can move large volumes of material, but they are less flexible and require precise scheduling. Delays can have a cascading effect on the supply chain.
- Efficiency: Rail is more efficient than road transport, especially for long-distance bulk transport, but not as continuous as a conveyor belt.
- Road Transport:
- Lower Efficiency: Road transport is less efficient, especially for bulk materials, due to lower capacity and higher fuel consumption. However, it offers flexibility for varying routes and delivery points.
- Capacity Limitations: Trucks have limited capacity compared to conveyor belts and trains, requiring more trips to move the same volume of material.
Overall Cost Comparison:
- Conveyor Belt: While the initial investment is high, the overall cost is lower in the long term due to low operating and maintenance costs, high efficiency, and minimal environmental impact. It’s the most cost-effective option for continuous bulk transport over a fixed route.
- Railway: Railways are cost-effective for long-distance bulk transport but come with higher initial and maintenance costs. They are less flexible and have higher operational costs than conveyor belts.
- Road Transport: Road transport has the lowest initial investment but the highest long-term costs due to high fuel consumption, maintenance, and environmental impact. It is less efficient for large-scale, continuous bulk transport over long distances.
For a large-scale, continuous operation like the Bou Craa phosphate mine, the conveyor belt is the most cost-effective and efficient solution compared to rail or road transport.

The Key of Where Can You Find the World’s Longest Conveyor Belt
Addressing the Phosphorus Conveyor Problem
The world’s longest conveyor belt is a marvel of engineering, stretching over 61 miles (98 kilometers) across the harsh desert landscape of Western Sahara. Known as the Bou Craa conveyor belt, it plays a crucial role in the mining and transportation of phosphate rock from the Bou Craa mine to the port city of El Aaiún. This remarkable structure highlights both the ingenuity of modern engineering and the significant challenges associated with transporting phosphorus, a vital component for agricultural fertilizers.
Environmental Concerns
One of the primary issues related to transporting phosphorus via the world’s longest conveyor belt involves environmental concerns. The Bou Craa conveyor belt transports a staggering 2,000 metric tons of phosphate rock every hour, making it a vital artery for the global agricultural industry. However, the environmental impact of this massive operation is considerable.
Phosphate mining and transportation can lead to significant environmental degradation. The extraction process often involves the removal of large amounts of overburden, which can disrupt local ecosystems and lead to soil erosion. Additionally, the dust generated during the mining and transportation process can have adverse effects on air quality. Dust particles can travel long distances, affecting both the environment and human health.
The conveyor belt itself, although an efficient means of transportation, poses its own environmental challenges. The belt runs through a fragile desert ecosystem, where any disruption can have lasting impacts. The constant movement of the belt and the transportation of large quantities of material can lead to habitat destruction and fragmentation, affecting local wildlife and plant species.
Logistical Challenges
The logistical challenges associated with maintaining and operating the world’s longest conveyor belt are significant. The Bou Craa conveyor belt operates in a harsh desert environment, where extreme temperatures, high winds, and sandstorms are common. These conditions can cause considerable wear and tear on the conveyor belt system, requiring regular maintenance and repairs to ensure its continued operation.
The sheer length of the conveyor belt also presents logistical challenges. With a length of 61 miles, any maintenance or repair work requires careful coordination and planning. The remote location of the conveyor belt adds to the complexity, as access to parts and equipment can be limited. Ensuring the continuous operation of the belt is critical, as any downtime can have significant economic repercussions.
Addressing Environmental and Logistical Concerns
Efforts are being made to address the environmental and logistical challenges associated with the world’s longest conveyor belt. To mitigate the environmental impact, measures such as dust suppression systems and environmental monitoring are being implemented. Dust suppression systems help to reduce the amount of dust generated during the mining and transportation process, thereby minimizing its impact on air quality. Environmental monitoring helps to track the impact of the conveyor belt on local ecosystems, allowing for timely interventions to mitigate any negative effects.
Logistically, advances in technology are playing a crucial role in maintaining the operation of the conveyor belt. Predictive maintenance systems, which use sensors and data analytics to monitor the condition of the conveyor belt, are being used to identify potential issues before they lead to system failures. This proactive approach helps to minimize downtime and ensures the continuous operation of the conveyor belt.
Economic Significance
The Bou Craa conveyor belt is not only a marvel of engineering but also an economic lifeline for the region. Phosphate rock is a critical component of agricultural fertilizers, and the efficient transportation of this material is essential for global food production. The conveyor belt allows for the efficient movement of large quantities of phosphate rock from the mine to the port, where it is then shipped to various destinations around the world.
The economic significance of the Bou Craa conveyor belt extends beyond the local region. The global agricultural industry relies heavily on the supply of phosphate rock for fertilizer production. Any disruption in the transportation of this material can have far-reaching consequences for food production and prices. Therefore, the efficient operation of the world’s longest conveyor belt is crucial for ensuring the stability of global food supplies.
Future Prospects
Looking to the future, there are ongoing efforts to improve the sustainability and efficiency of the Bou Craa conveyor belt. Research is being conducted into the use of alternative materials and technologies that can reduce the environmental impact of phosphate mining and transportation. Innovations in conveyor belt design and materials are also being explored to improve the durability and longevity of the system.
Furthermore, there is a growing emphasis on the need for sustainable mining practices. Companies and governments are increasingly recognizing the importance of minimizing the environmental impact of mining operations. This includes implementing measures to protect local ecosystems, reduce emissions, and promote the responsible use of natural resources.
How to Know Where Can You Find the World’s Longest Conveyor Belt
Inside the Largest Phosphate Mine in the World
When you ask, “where can you find the world’s longest conveyor belt,” the journey leads you to the vast expanse of the Western Sahara. Here lies the Bou Craa mine, renowned not only for housing the longest conveyor belt but also for being one of the largest phosphate mines in the world. This mine plays a pivotal role in the global phosphorus supply chain, significantly impacting agriculture and industry worldwide.
The Significance of the Bou Craa Phosphate Mine
The Bou Craa mine is an integral part of Morocco’s mining industry, even though it is located in the disputed territory of Western Sahara. Phosphates mined here are essential for producing fertilizers, which are crucial for modern agriculture. Phosphorus, derived from phosphates, is a key nutrient required for plant growth. As global food demand continues to rise, the importance of phosphates in supporting agricultural productivity cannot be overstated.
The Bou Craa mine is operated by the state-owned company OCP (Office Chérifien des Phosphates), which controls the majority of the world’s phosphate reserves. The mine’s contribution to the global phosphate market underscores its significance in maintaining a steady supply of this critical mineral.
Production Capacity and Operations
The Bou Craa mine boasts impressive production capacity. It is estimated to produce several million tons of phosphate rock annually. The mining process involves extracting phosphate ore from the earth, which is then crushed and processed to produce phosphate rock. This raw material is used in the manufacture of phosphate fertilizers and other phosphorus-based products.
The mining operations at Bou Craa are extensive, covering a large area of the Western Sahara desert. The extracted phosphate is transported via the world’s longest conveyor belt, a 98-kilometer (61-mile) marvel of engineering that stretches from the mine to the port of El Aaiún. This conveyor belt significantly enhances the efficiency of the mining operations, enabling the rapid and cost-effective transport of phosphate to the coast for export.
The Role of the Conveyor Belt
Where can you find the world’s longest conveyor belt? The answer is intertwined with the Bou Craa mine. This conveyor belt is a critical component of the mine’s infrastructure, designed to move vast quantities of phosphate across the desert. Its existence underscores the importance of efficient logistics in large-scale mining operations.
The conveyor belt itself is a testament to human ingenuity. Constructed from durable materials designed to withstand the harsh desert environment, it comprises a series of interconnected belts powered by electric motors. The system includes multiple pulleys and rollers, ensuring the belt operates smoothly over its entire length. Advanced monitoring systems are in place to detect any potential issues, allowing for timely maintenance and repairs.
Global Impact of Phosphate from Bou Craa
The phosphate extracted from the Bou Craa mine has far-reaching impacts on the global agricultural industry. Phosphate fertilizers are essential for enhancing soil fertility and boosting crop yields. As such, the phosphates from Bou Craa play a vital role in supporting global food production.
Countries around the world rely on phosphate imports to meet their agricultural needs. The Bou Craa mine’s production capacity and its efficient transport system ensure a steady supply of phosphates to international markets. This reliability is crucial for maintaining the stability of the global food supply chain, particularly as demand for agricultural products continues to grow.
Environmental and Social Considerations
While the Bou Craa mine and its conveyor belt are engineering marvels, their environmental and social impacts are significant. The mining operations and the conveyor belt traverse sensitive desert ecosystems, potentially affecting local flora and fauna. Efforts are made to mitigate these impacts, including implementing dust suppression systems and minimizing emissions from mining and transport activities.
Moreover, the political and social implications of mining in Western Sahara are complex. The territory is subject to an ongoing dispute between Morocco and the indigenous Sahrawi people. The exploitation of natural resources in this region is a contentious issue, with calls for ensuring that local populations benefit from the economic activities taking place on their land.
Technological Innovations and Future Prospects
The technological advancements employed at the Bou Craa mine and its conveyor belt system are continually evolving. Innovations in materials science, automation, and environmental management are driving improvements in efficiency and sustainability. For instance, the use of predictive maintenance technologies helps to minimize downtime and extend the lifespan of the conveyor belt, ensuring it operates at peak efficiency.
Looking to the future, further advancements are expected to enhance the performance of the Bou Craa mine. Continued research and development in mining technologies will likely lead to more efficient extraction and processing methods. Additionally, efforts to reduce the environmental impact of mining operations will play a crucial role in promoting sustainable practices.

The Types of Where Can You Find the World’s Longest Conveyor Belt
A Closer Look at the Bou Craa Phosphate Mine
If you’re wondering where can you find the world’s longest conveyor belt, you need to look no further than the Bou Craa phosphate mine in Western Sahara. This remarkable conveyor belt, stretching over 61 miles (98 kilometers), is a testament to modern engineering and plays a crucial role in the operations of the Bou Craa phosphate mine. Let’s delve deeper into the mine’s operations, its significance to the region, and its contribution to the global phosphate reserves.
The Operations of Bou Craa Phosphate Mine
The Bou Craa phosphate mine, located in the heart of the Western Sahara desert, is one of the largest phosphate mines in the world. The mining operations here are extensive, involving the extraction of massive quantities of phosphate rock. The phosphate ore is found in a sedimentary deposit that is part of the extensive Eocene geological formation, which spans across much of North Africa.
Mining operations at Bou Craa are highly mechanized, utilizing advanced equipment and technologies to extract and process the phosphate rock efficiently. The extracted phosphate rock is first crushed and then transported via the world’s longest conveyor belt to the coastal city of El Aaiún, where it is prepared for export.
The conveyor belt system is an engineering marvel, designed to operate continuously in the harsh desert environment. It consists of several segments, each powered by electric motors, and is capable of transporting up to 2,000 metric tons of phosphate rock per hour. The belt itself is made from a durable rubber material that can withstand the extreme temperatures and abrasive conditions of the desert.
Importance to the Region
The Bou Craa phosphate mine is of immense importance to the region, both economically and socially. It is one of the primary sources of employment in the area, providing jobs for thousands of local workers. The mining operations have also spurred the development of infrastructure, including roads, housing, and healthcare facilities, thereby improving the quality of life for the local population.
Economically, the Bou Craa mine is a significant contributor to the economy of Western Sahara. Phosphate rock is a valuable commodity, used primarily in the production of agricultural fertilizers. The revenue generated from the export of phosphate rock provides a vital source of income for the region, supporting various public services and development projects.
The presence of the world’s longest conveyor belt has also become a symbol of technological prowess and innovation, showcasing the ability to overcome logistical challenges in one of the most inhospitable environments on the planet.
Contribution to the World’s Phosphate Reserves
Phosphate rock is an essential resource for global agriculture, used in the production of fertilizers that are crucial for crop growth. The Bou Craa mine is one of the largest producers of phosphate rock, contributing significantly to the world’s phosphate reserves. The high-quality phosphate rock extracted from Bou Craa is rich in phosphorus content, making it highly sought after by fertilizer manufacturers worldwide.
The global demand for phosphate rock continues to grow as the world’s population increases and the need for food production intensifies. The Bou Craa mine plays a critical role in meeting this demand, ensuring a steady supply of phosphate rock to international markets. The efficient transportation system, highlighted by the world’s longest conveyor belt, is key to maintaining the steady flow of this vital resource.
Environmental and Operational Challenges
Operating a massive mining operation in the harsh desert environment of Western Sahara presents numerous challenges. The Bou Craa phosphate mine, along with its conveyor belt system, faces extreme temperatures, sandstorms, and the abrasive nature of the desert sand. These conditions can cause significant wear and tear on the equipment, necessitating regular maintenance and repairs.
Environmental concerns also arise from the large-scale extraction and transportation of phosphate rock. The mining process can disrupt local ecosystems, and the transportation of phosphate rock can generate dust and other pollutants. Efforts are being made to mitigate these environmental impacts through the implementation of dust suppression systems, environmental monitoring, and sustainable mining practices.
Technological advancements are helping to address some of these challenges. Predictive maintenance systems, using sensors and data analytics, are employed to monitor the condition of the conveyor belt and other equipment, allowing for timely interventions to prevent breakdowns. This proactive approach helps to minimize downtime and ensures the continuous operation of the mining and transportation system.
Future Prospects and Innovations
Looking ahead, there are ongoing efforts to improve the sustainability and efficiency of the Bou Craa phosphate mine and its conveyor belt system. Research is being conducted into the use of alternative materials and technologies that can reduce the environmental impact of phosphate mining and transportation. Innovations in conveyor belt design and materials are also being explored to enhance durability and longevity.
Sustainable mining practices are becoming increasingly important as companies and governments recognize the need to minimize the environmental impact of mining operations. This includes measures to protect local ecosystems, reduce emissions, and promote the responsible use of natural resources.
Furthermore, there is a growing emphasis on social responsibility and community engagement. Mining companies are working closely with local communities to ensure that the benefits of mining operations are shared equitably and that the rights and well-being of local populations are respected.
The Ways of Where Can You Find the World’s Longest Conveyor Belt
Engineering Innovations in Conveyor Belt Design
The construction of the world’s longest conveyor belt required a series of groundbreaking engineering innovations. The harsh desert environment of Western Sahara presented numerous challenges, including extreme temperatures, sandstorms, and difficult terrain. To overcome these obstacles, engineers employed advanced materials and cutting-edge technologies.
One of the key innovations was the use of reinforced rubber belts designed to withstand the abrasive nature of the desert sand. These belts are constructed with multiple layers of rubber and fabric, providing the necessary strength and durability to handle the constant wear and tear. Additionally, special coatings are applied to the belts to reduce friction and heat buildup, ensuring smooth and efficient operation over long distances.
Structural and Mechanical Components
The structural integrity of the conveyor belt system is maintained by a network of steel support structures and towers. These structures are strategically placed along the route to provide stability and support, especially in areas with challenging terrain. The towers are anchored into the ground using deep foundations, ensuring they remain secure even during strong winds and sandstorms.
Mechanical components such as pulleys, rollers, and motors are essential for the operation of the conveyor belt. The pulleys are designed to handle the immense weight and tension of the belt, while the rollers reduce friction and support the belt’s movement. Powerful electric motors drive the entire system, providing the necessary force to transport the phosphate over long distances. These motors are equipped with advanced control systems that monitor and adjust the belt’s speed and tension, optimizing performance and preventing breakdowns.
Technological Advancements in Monitoring and Maintenance
Technological advancements have played a crucial role in the efficient operation and maintenance of the world’s longest conveyor belt. Automated control systems and sensors are integrated into the belt’s infrastructure to monitor its performance in real-time. These systems collect data on various parameters such as belt speed, tension, temperature, and wear, allowing for proactive maintenance and early detection of potential issues.
Predictive maintenance technologies use data analytics and machine learning algorithms to analyze the collected data and predict when maintenance is required. This approach minimizes downtime and reduces maintenance costs by addressing issues before they become critical. Remote monitoring capabilities also enable engineers to oversee the conveyor belt’s operation from a central control room, making it easier to manage and maintain the system.
Environmental and Economic Impact
Where can you find the world’s longest conveyor belt? In Western Sahara, this belt not only serves a critical function in the phosphate mining industry but also has significant environmental and economic impacts. By providing a highly efficient means of transporting phosphate, the conveyor belt reduces the need for truck or rail transport, lowering greenhouse gas emissions and minimizing environmental disruption.
Economically, the conveyor belt enhances the productivity and profitability of the Bou Craa mine. The efficient transport system ensures a steady supply of phosphate to international markets, supporting global agriculture and food production. The mine’s operations generate revenue and provide employment opportunities, contributing to the economic development of the region.
Future Prospects and Innovations
The future of long conveyor belts holds promise for further advancements in engineering and technology. Innovations in materials science, such as the development of more durable and lightweight materials, will enhance the performance and lifespan of conveyor belts. Advances in automation and control systems will continue to improve efficiency and reduce maintenance requirements.
Environmental sustainability will also be a key focus, with efforts to develop eco-friendly materials and technologies that minimize the environmental impact of conveyor belt systems. Renewable energy sources, such as solar and wind power, may be integrated into the operation of conveyor belts, reducing their carbon footprint and promoting sustainable mining practices.
FAQS about Where Can You Find The World’s Longest Conveyor Belt
The longest conveyor belt in the world is located in the Western Sahara, stretching over 61 miles (98 kilometers) from the phosphate mines of Bu Craa to the coast south of El-Aaiun. This impressive structure is a critical part of the phosphate mining process, transporting vast quantities of material efficiently. The belt is not only an engineering marvel but also a vital infrastructure component that supports the local economy and industry. Its location in a remote, arid region underscores the significant challenges and achievements involved in its construction and operation.
The world record for the longest conveyor belt is held by the belt in the Western Sahara, spanning 61 miles (98 kilometers). This conveyor belt is a testament to human ingenuity and the ability to overcome logistical challenges in transporting materials across great distances. The belt’s design and implementation have set a high standard in the field of conveyor technology, showcasing how advanced engineering can achieve remarkable feats. Its role in the efficient movement of phosphate from mines to ports underscores its importance in global supply chains and industrial processes.
The world’s largest conveyor belt company is ContiTech, a division of Continental AG. Known for their innovation and quality, ContiTech leads the market in manufacturing and supplying high-performance conveyor belts used across various industries, including mining, automotive, and industrial applications. The company’s extensive portfolio and global presence highlight its capability to deliver tailored solutions that meet the diverse needs of its clients. ContiTech’s commitment to research and development ensures that they remain at the forefront of technological advancements in conveyor belt systems.
The longest conveyor in Australia is the Curragh overland conveyor, which stretches over 20 kilometers. This conveyor belt is a vital part of the Curragh coal mine operations in Queensland, efficiently transporting coal from the mine to the processing plant. The design and implementation of such a long conveyor system in Australia highlight the country’s advanced mining infrastructure and commitment to efficient resource management. The Curragh conveyor exemplifies how long-distance conveyor belts can significantly enhance operational efficiency and productivity in the mining sector.
The world’s longest conveyor belt is located in the Western Sahara. It is approximately 98 kilometers (61 miles) long and is used to transport phosphate from the Bou Craa mine to the coast near El Aaiún, from where it is shipped internationally.
The “great conveyor belt” typically refers to the thermohaline circulation of the world’s oceans, also known as the Global Ocean Conveyor Belt. This vast system of ocean currents, driven by differences in water temperature and salinity, circulates through all of the world’s oceans, playing a critical role in regulating the Earth’s climate.
The longest conveyor belt in Texas is located at the North American Coal Corporation’s Sabine Mine in Hallsville. It stretches for over 5 miles (8 kilometers) and is used to transport lignite coal to the nearby power plant.
Last Updated on October 18, 2024 by Jordan Smith
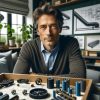
Jordan Smith, a seasoned professional with over 20 years of experience in the conveyor system industry. Jordan’s expertise lies in providing comprehensive solutions for conveyor rollers, belts, and accessories, catering to a wide range of industrial needs. From initial design and configuration to installation and meticulous troubleshooting, Jordan is adept at handling all aspects of conveyor system management. Whether you’re looking to upgrade your production line with efficient conveyor belts, require custom conveyor rollers for specific operations, or need expert advice on selecting the right conveyor accessories for your facility, Jordan is your reliable consultant. For any inquiries or assistance with conveyor system optimization, Jordan is available to share his wealth of knowledge and experience. Feel free to reach out at any time for professional guidance on all matters related to conveyor rollers, belts, and accessories.