Leading Manufacturers of White Rubber Conveyor Belt
A white rubber conveyor belt is a versatile option widely used across various industries. These belts are ideal for applications requiring strict hygiene standards, such as food processing and pharmaceuticals. With anti-static, oil-resistant, and high-temperature properties, white rubber conveyor belts come in different sizes, coatings, and configurations to suit diverse operational needs. Their bright color aids in identifying contamination, ensuring a clean and safe production line.
Benefits of Using White Rubber Conveyor Belt in Manufacturing
In the vast world of conveyor belts, white rubber conveyor belts stand out for their unique properties and specific uses in various manufacturing sectors. Recognized for their cleanliness and non-marking nature, white rubber conveyor belts are particularly valued in industries where hygiene and product purity are of utmost importance. This detailed discussion explores the numerous advantages that white rubber conveyor belts bring to manufacturing processes, highlighting why many sectors prefer them over other types of belts.
Non-Marking Nature
One of the primary benefits of using a white rubber conveyor belt is its non-marking property. Unlike black rubber belts that can leave marks on transported goods, white rubber belts are made from compounds that prevent marking. This feature is crucial in industries such as:
- Food and Beverage: Ensuring that products do not have any smudge or color contamination from the belts.
- Pharmaceuticals: Maintaining the pristine condition of products during processing and packaging.
- Electronics: Protecting sensitive components from any potential abrasion marks that could affect functionality.
Hygienic Properties
The hygienic properties of white rubber conveyor belts are particularly advantageous for applications requiring stringent cleanliness standards. The white rubber material is often resistant to microbial growth and easy to clean, making it ideal for sectors such as:
- Food Processing: White rubber belts can be sanitized effectively, ensuring that the food contact surface remains free from pathogens and contamination.
- Packaging Industries: Keeping the conveyor system free from contaminants that could transfer to the packaging material and, subsequently, to the consumer.
High Visibility for Safety and Quality Control
The bright white color of these conveyor belts offers high visibility, which is essential for safety and quality control in manufacturing environments. Operators can easily spot product pieces or contaminants that might compromise the product quality or pose safety risks, such as:
- Metal shavings
- Broken parts of machinery
- Other foreign objects
This visibility makes it easier to maintain a controlled and safe manufacturing process, which is critical in high-speed production lines where manual inspection needs to be prompt and efficient.
Chemical and Abrasion Resistance
White rubber conveyor belts are typically manufactured to be resistant to various chemicals and abrasives. This makes them suitable for handling:
- Chemical Products: Certain types of white rubber belts are designed to resist degradation from chemicals, oils, and other substances that could otherwise deteriorate a standard belt.
- Harsh Environments: Industries like chemical processing or metalworking, where the conveyor belt may come into contact with corrosive materials or sharp objects.
Temperature Resistance
Another significant advantage of white rubber conveyor belts is their ability to withstand different temperatures. This is particularly beneficial in industries like food processing, where belts may need to endure high temperatures during baking or freezing during product handling. White rubber belts are designed to:
- Withstand high temperatures without losing integrity or elasticity.
- Remain flexible at low temperatures to prevent cracking or brittleness, which could lead to belt failure.
Aesthetic and Regulatory Compliance
In many cases, the aesthetic aspect of white rubber conveyor belts is preferred for certain products and environments. Additionally, these belts often comply with various regulatory standards set for different industries, ensuring that they meet the safety, health, and environmental regulations. This is particularly critical in:
- Food production: Where FDA (Food and Drug Administration) approval might be necessary.
- Pharmaceutical manufacturing: Where adherence to health standards cannot be compromised.
Cost-Effectiveness
Despite their specialized attributes, white rubber conveyor belts can be cost-effective solutions due to their durability and extended service life. The initial investment in a high-quality white rubber conveyor belt often pays off in the long term by reducing the need for frequent replacements and maintenance.
White rubber conveyor belts offer a range of benefits that make them a preferred choice in many manufacturing sectors. From their non-marking nature and hygienic properties to their high visibility and resistance to harsh conditions, these belts enhance both the efficiency and safety of production processes. Industries prioritizing cleanliness, safety, and compliance find significant value in adopting white rubber conveyor belts, making them integral components of modern manufacturing operations.
Key Features of White Rubber Conveyor Belt
White rubber conveyor belts are a specialized category of conveyor belts designed for specific industrial applications where hygiene, visibility, and non-marking properties are critical. The unique characteristics of white rubber conveyor belts make them ideal for use in food processing, pharmaceuticals, and other sectors where cleanliness is paramount. This detailed exploration will discuss the various properties of white rubber conveyor belts and why they are chosen for these particular applications.
Hygienic Properties
The primary advantage of white rubber conveyor belts is their hygienic properties. White rubber is often manufactured to be non-toxic and food-grade, complying with international food contact regulations such as the FDA (Food and Drug Administration) in the United States and the EU’s Regulation (EC) No 1935/2004. This makes white rubber belts suitable for direct contact with food products during processing and packaging.
- Easy to Clean: The smooth surface of white rubber belts allows for easier cleaning and disinfection, which is essential in food processing and pharmaceutical industries to prevent contamination and maintain product purity.
- Resistance to Microbial Growth: Many white rubber conveyor belts are treated with antimicrobials to inhibit the growth of bacteria and mold, further enhancing their suitability for stringent hygienic conditions.
Visibility and Safety
Another significant feature of white rubber conveyor belts is their high visibility. The bright white color provides a stark contrast against most foods and industrial products, making it easier to identify product fragments and contaminants on the belt.
- Enhanced Safety: The increased visibility of white belts helps in monitoring product handling more effectively, ensuring that any issues can be spotted and addressed quickly, thereby reducing the risk of contamination.
- Product Integrity: In industries where product appearance is crucial, such as in the baking or confectionery sectors, the non-marking nature of white rubber ensures that products remain clean and presentable throughout the processing line.
Durability and Performance
Despite their specific coloration, white rubber conveyor belts do not sacrifice performance for aesthetics. These belts are designed to offer durability and efficient handling capabilities similar to their black rubber counterparts.
- Wear Resistance: White rubber conveyor belts are formulated to withstand the abrasive actions of product handling, which extends their operational life and reduces the frequency of belt replacements.
- Chemical Resistance: These belts often possess resistance to various chemicals, making them suitable for industries where exposure to fats, oils, and other aggressive substances is common.
Temperature Resistance
White rubber conveyor belts are also capable of handling extreme temperatures, which is particularly important in baking and food processing industries.
- Heat and Cold Resistance: These belts can operate effectively in environments with varying temperatures, from the heat of ovens to the cold of freezers, without losing flexibility or strength.
Custom Solutions by White Rubber Conveyor Belt Manufacturers
Tailored Manufacturing to Meet Specific Industrial Demands
In the diverse world of industrial manufacturing, the need for customized solutions is ever-present. This is especially true in the case of conveyor systems, where the specific demands of different industries can vary greatly. White rubber conveyor belts are particularly sought after for their clean, non-marking properties, which make them ideal for sectors like food processing, pharmaceuticals, and electronics manufacturing. This article explores how manufacturers of white rubber conveyor belts tailor their products to meet the unique business needs of various industries, ensuring optimal performance and compliance with industry standards.
Demand for Custom White Rubber Conveyor Belts
White rubber conveyor belts are not only preferred for their aesthetic cleanliness but also for their operational characteristics. They provide high visibility, are easy to clean, and meet stringent regulatory requirements, making them suitable for industries that prioritize hygiene and safety. The demand for custom solutions arises because each application may have different operational environments, load requirements, and safety standards.
Customization Processes of White Rubber Conveyor Belts
1. Material Composition Adjustments
One of the primary customization options offered by manufacturers is the adjustment of material compositions to enhance specific properties of the conveyor belt such as:
- Resistance to Oils and Chemicals: For industries such as chemical processing or parts manufacturing where oils and chemicals are prevalent, belts can be made resistant to these substances to prevent degradation.
- Temperature Resistance: In food processing or pharmaceuticals, where belts may be subjected to high or low temperatures, materials are customized to withstand these extremes without losing structural integrity.
- Antimicrobial Properties: Especially important in the food and pharmaceutical sectors, conveyor belts can be infused with antimicrobial agents to inhibit the growth of bacteria and mold, promoting a sanitary environment.
2. Belt Design Customization
The design of the conveyor belt is often customized to suit specific operational needs. This includes:
- Belt Width and Thickness: Depending on the load to be transported and the physical layout of the plant, belts can be made wider or thicker.
- Profile Modifications: Raised profiles, cleats, or guided ribs might be added to the belt to suit particular transport conditions or to handle specific types of materials more effectively.
3. Reinforcement Options
To enhance the durability and longevity of white rubber conveyor belts, manufacturers offer various reinforcement options:
- Fabric Layers: For added strength and reduced stretch, additional layers of fabric can be embedded within the rubber.
- Metal Reinforcements: In heavy-duty applications where belts need to carry particularly heavy loads, steel cords or mesh can be incorporated for extra strength.
4. Edge Sealing and Surface Treatments
Custom solutions also involve modifications to the belt edges and surfaces:
- Edge Sealing: To prevent fraying and ensure cleaner operations, the edges of the belts can be sealed.
- Surface Treatments: Depending on the application, the belt surface might be textured to increase grip or smoothed to allow for easier cleaning.
Collaboration and Consultation in Customization
The process of customizing white rubber conveyor belts typically involves close collaboration between the manufacturer and the client. This process includes:
- Consultation: Initial discussions to understand the specific requirements of the client, including environmental challenges, load specifications, and any regulatory compliance needs.
- Prototyping: In some cases, prototypes or small batches of the customized belt are produced and tested under operational conditions to ensure they meet the expected performance criteria.
- Feedback and Refinement: Based on feedback received from the testing phase, further refinements may be made to optimize the belt’s design and functionality.
Manufacturers of white rubber conveyor belts provide a broad range of customization options to meet the specific needs of different industries. By adjusting material compositions, modifying belt designs, and adding specialized features, they ensure that each conveyor belt is perfectly suited to its intended application. This tailored approach not only enhances the operational efficiency of conveyor systems but also ensures compliance with industry-specific standards, ultimately contributing to higher productivity and safety in various manufacturing environments. Through innovative engineering and collaborative design processes, manufacturers are able to deliver conveyor belt solutions that precisely match the unique demands of their clients.
Top White Rubber Conveyor Belt Manufacturers
In the competitive market of industrial conveyor systems, several manufacturers stand out for their high-quality white rubber conveyor belts. These companies are recognized for their innovation, reliability, and comprehensive range of products tailored to meet the specific needs of industries requiring hygienic conveyor solutions.
1. Habasit
Overview: Habasit is a leading global manufacturer known for its broad range of conveyor and processing belts. The company specializes in belts for food processing and other hygiene-sensitive industries.
Product Offerings: Habasit’s portfolio includes a variety of white food-grade conveyor belts that meet both national and international standards. These belts are designed for applications requiring excellent chemical and microbial resistance.
2. Intralox
Overview: Intralox is renowned for its innovative modular belt solutions, which include a range of white rubber conveyor belts specifically designed for food industries.
Product Offerings: Intralox offers hygienic belt solutions that are easy to clean and maintain, with specialized surfaces that enhance product handling and decrease product loss.
3. Ammeraal Beltech
Overview: Ammeraal Beltech operates globally, providing high-quality conveyor belting solutions for various sectors. The company focuses on belts that offer durability and food safety.
Product Offerings: Ammeraal Beltech’s white rubber conveyor belts are engineered for performance and hygiene, suitable for a wide range of food processing applications from bakery to meat and poultry.
White rubber conveyor belts represent a critical component in industries where hygiene, safety, and visibility are paramount. The unique properties of these belts, combined with the expertise of leading manufacturers, ensure that they continue to be the preferred choice for businesses looking to maintain the highest standards of cleanliness and efficiency in their operations. Whether in food processing, pharmaceuticals, or other sensitive environments, white rubber conveyor belts provide a reliable and effective solution for handling products with care and precision.
Used White Rubber Conveyor Belt: What You Need to Know
When it comes to efficiency and cost-effectiveness in material handling, conveyor belts are indispensable in a variety of industrial applications. Specifically, white rubber conveyor belts are favored in sectors that require high standards of hygiene and visibility, such as food processing and pharmaceuticals. Opting for used white rubber conveyor belts can offer substantial benefits, including reduced costs and environmental impact. However, understanding the nuances of purchasing and utilizing used white rubber conveyor belts is crucial to making the most of their potential. This detailed guide explores the important considerations you should keep in mind when acquiring used white rubber conveyor belts, including potential uses and tips for thorough evaluation.
Evaluating the Suitability of Used White Rubber Conveyor Belts
1. Assessing Quality and Condition
The longevity and functionality of a white rubber conveyor belt heavily depend on its condition at the time of purchase. Here are key aspects to evaluate:
- Surface Wear and Tears: Examine the belt thoroughly for any signs of excessive wear, tears, or cuts, especially since white rubber can show stains and marks more clearly than darker materials. Minor wear might be acceptable, but deep cuts or significant abrasions can compromise the belt’s integrity.
- Cleanliness: Given that white rubber belts are often used in applications requiring strict hygiene, assess how well the belt has been cleaned and maintained. Residue from previous use can be a contamination risk.
- Elasticity and Flexibility: Check the elasticity of the belt. Rubber can become stiff and lose its flexibility over time, particularly if it has been exposed to temperature extremes or chemicals.
2. Understanding Previous Usage
Knowing the history of the conveyor belt is crucial. The type of environment and materials the belt was exposed to previously can significantly impact its future performance:
- Type of Materials Transported: If the belt was used to transport abrasive materials, it might be more prone to wear and less suitable for delicate applications.
- Operating Conditions: Belts used in harsh environments, such as extreme temperatures or exposure to chemicals, may have reduced lifespans.
3. Potential for Repurposing
Consider whether the belt can be repurposed for different applications than originally intended. White rubber conveyor belts used in food processing might also be suitable for packaging or assembly lines in other industries, provided they meet hygiene and safety standards.
Tips for Evaluation
- Consult with Experts: If possible, involve a technician or an expert in conveyor systems when evaluating the belt. Their expertise can help identify potential issues that may not be apparent at first glance.
- Request Documentation: Ask for any available maintenance logs, repair records, or quality certifications from the seller to better understand the belt’s history and upkeep.
- Inspect in Person: Whenever possible, inspect the belt in person rather than relying on pictures or descriptions online. This can help you assess the true condition of the belt more accurately.
Maintenance Tips for White Rubber Conveyor Belt
Maintaining white rubber conveyor belts not only extends their lifespan but also ensures they perform optimally throughout their service life. Proper maintenance is particularly crucial for white belts due to their visible nature and the industries they are typically used in, which often require high standards of cleanliness and functionality.
Regular Cleaning and Inspection
- Routine Cleaning: Regular cleaning is essential to maintain the hygienic condition of white rubber conveyor belt, especially in food processing or pharmaceutical applications. Use appropriate cleaning agents that are effective yet gentle enough not to degrade the rubber.
- Frequent Inspections: Conduct regular inspections to catch potential issues early, such as small tears or wear spots before they develop into more significant problems. Pay particular attention to the edges and joints of the belt.
Proper Storage and Handling
- Storage Conditions: Store spare white rubber conveyor belts in a cool, dry place away from direct sunlight, which can cause rubber to deteriorate and discolor. Ensure the storage area is clean to avoid contamination.
- Handling Practices: When installing or repairing the belt, handle it with care to avoid unnecessary stress or damage. Use the right tools and follow manufacturer guidelines for tensioning and tracking to ensure the belt runs smoothly.
Use of Appropriate Accessories
- Tracking and Tensioning Systems: Employ proper tracking and tensioning systems to prevent misalignment, which can wear out the belt prematurely. Regularly check these systems to ensure they function correctly.
- Sealing and Edge Protection: Consider using sealing or edge protection, especially in environments where the belt might be exposed to particulates or liquids that could cause wear or contamination.
Used white rubber conveyor belts can provide significant cost savings and flexibility for various industrial applications. However, careful selection, thorough evaluation, and diligent maintenance are essential to maximize their value and ensure safe, efficient operation. By following these guidelines, businesses can effectively incorporate used white rubber conveyor belts into their operations, achieving both economic and environmental benefits.
Recycling and Sustainability Practices with White Rubber Conveyor Belt
The recyclability and environmental impact of white rubber conveyor belts are increasingly important considerations for industries. Sustainable practices and innovations have made significant strides, ensuring that white rubber conveyor belts can have a reduced environmental footprint and an extended life cycle.
- Recyclability of White Rubber Conveyor Belts
White rubber conveyor belts are recyclable, especially those manufactured from high-quality materials. Manufacturers can reclaim the rubber and other components, using them in the production of new belts or other rubber-based products. Companies specializing in belt recycling use advanced processes to minimize waste and reduce the burden on landfills. - Environmental Impact of Production
The production of white rubber conveyor belts adheres to strict environmental standards. This includes minimizing volatile organic compounds (VOCs) and harmful chemicals during manufacturing. Sustainable production methods, such as using renewable energy and reducing water waste, further enhance the green credentials of these conveyor belts. - Sustainable Design
Modern white rubber conveyor belts are engineered to be highly durable, which extends their operational life and reduces the need for frequent replacements. This resilience minimizes waste and decreases the carbon footprint associated with the manufacturing and shipping of new belts. - Reuse Practices
Even after their primary life cycle, white rubber conveyor belts can find new applications. Many industries repurpose used belts as protective floor mats, vehicle liners, or barriers in heavy-duty areas. This reuse helps companies save costs and contributes to circular economy practices. - Corporate Responsibility and Innovation
Conveyor belt manufacturers are increasingly prioritizing sustainability in their corporate social responsibility strategies. They focus on developing greener technologies and reducing their overall environmental impact. Additionally, collaborations between manufacturers and recycling companies foster innovative approaches to reusing materials. - Compliance with Environmental Regulations
The production and disposal of white rubber conveyor belts are governed by various environmental regulations. These guidelines ensure proper disposal and recycling practices to prevent environmental contamination. Many manufacturers proactively align their operations with these standards, ensuring their products contribute positively to sustainability goals. - Overall, white rubber conveyor belt is becoming more eco-friendly, with improvements in recyclability and sustainability practices. Through responsible production, reuse, and recycling, these belts minimize waste while maximizing their value in various industrial applications. Investing in environmentally conscious conveyor belts benefits not only businesses but also our planet, by supporting sustainable resource management and reducing industrial waste.
FAQs about White Rubber Conveyor Belt
Conveyor belts are typically made from two main types of rubber, chosen for their specific properties that suit different handling needs. The most common types of rubber used include:
Natural Rubber: Known for its excellent tensile strength and elasticity, natural rubber is often used in conveyor belts that require flexibility and durability. It’s particularly effective in environments where the belts are subjected to high impact and wear.
Synthetic Rubber: This category includes several types of rubber, each selected based on the specific needs of the conveyor belt application:
Styrene Butadiene Rubber (SBR): Often used for its good abrasion resistance and is typically more affordable than other rubbers. It performs well in general-purpose applications but is not suitable for oil or chemical-heavy environments.
Nitrile Rubber (NBR): Known for its excellent oil resistance, making it ideal for industries where oils, greases, and fats are prevalent, such as food processing or chemicals manufacturing.
Ethylene Propylene Diene Monomer (EPDM): Chosen for its outstanding resistance to heat, weathering, and chemicals, making it suitable for outdoor conveyor systems.
Conveyor belts can come in various colors, each typically serving a specific purpose or industry requirement:
Black: The most common color, especially for rubber belts, as carbon black is added for UV protection and strength.
White: Often used in food processing industries where it is essential to easily see contamination and maintain a high standard of hygiene.
Green: Sometimes used in the materials handling industries to signify specific properties, such as antistatic characteristics.
Blue: Frequently used in food processing facilities because blue is a color not commonly found in food, making contamination visible.
There are several types of belt conveyors used across various industries, each designed for specific applications:
Flat Belt Conveyors: The most common type, used to transport light to medium loads, whether in a horizontal or inclined path.
Modular Belt Conveyors: Made of plastic composite materials, making them more durable, versatile, and suitable for transporting items in various environments.
Cleated Belt Conveyors: These conveyors have vertical cleats or barriers that help control product spillage, ideal for incline or decline transportation.
Curved Belt Conveyors: Designed to navigate curves and change the direction of the conveyor path while maintaining the orientation and stability of the product.
Rubber conveyor belts come in a variety of sizes tailored to meet the needs of different applications and machinery. The size of a conveyor belt is typically characterized by its length, width, and thickness, which can vary significantly:
Width: Conveyor belt widths are usually measured in millimeters or inches, ranging widely from about 300 mm (12 inches) up to 2000 mm (78 inches) or more, depending on the application.
Length: The length of conveyor belts can vary from a few meters up to several kilometers in the case of mining conveyors.
Thickness: The thickness of the belt depends on the operational demands and the materials being transported. It typically ranges from 5 mm to over 30 mm.
Last Updated on July 16, 2024 by Jordan Smith
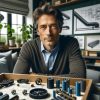
Jordan Smith, a seasoned professional with over 20 years of experience in the conveyor system industry. Jordan’s expertise lies in providing comprehensive solutions for conveyor rollers, belts, and accessories, catering to a wide range of industrial needs. From initial design and configuration to installation and meticulous troubleshooting, Jordan is adept at handling all aspects of conveyor system management. Whether you’re looking to upgrade your production line with efficient conveyor belts, require custom conveyor rollers for specific operations, or need expert advice on selecting the right conveyor accessories for your facility, Jordan is your reliable consultant. For any inquiries or assistance with conveyor system optimization, Jordan is available to share his wealth of knowledge and experience. Feel free to reach out at any time for professional guidance on all matters related to conveyor rollers, belts, and accessories.